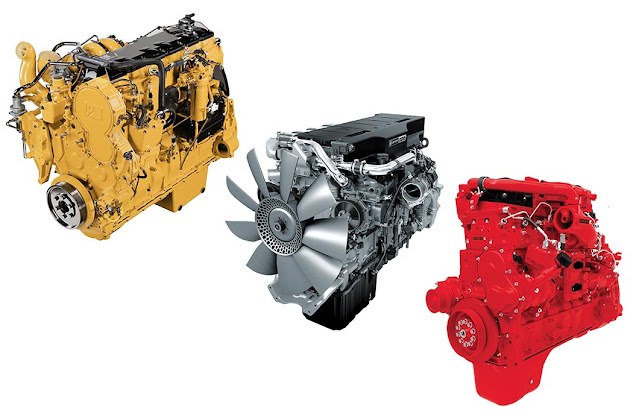
with engine emissions a critical subject in both the industrialized world and developing nations, the Society of Automotive Engineers (SAE) International's Heavy Duty Diesel Emissions Control Symposium, held recently in Gothenburg,Sweden, proved to be an interesting forum for those interested in a cleaner environment. The event gathered around 300 people who were a mix of engine and system manufacturers,plus a variety of specialists in the area of emissions control, research bodies and the general populace.
Approximately 15 companies and organizations presented papers, and the three symposium sponsors Johnson Matthey, Volvo and Corning Inc. all presented papers outlining their products and services. The two day program created great interest and sparked lots of questions and discussions during panel sessions. In a foreword to the event, the organizers pointed to the original equipment
emissions control regulations, soon to be enforced, making control of heavy-duty diesel (HDD) a top priority.
Consequently, the symposium highlighted legislation, the implications and challenges of compliance. Emissions control strategies, engine design and affertreatment technologies were discussed from a global perspective, as were the health effects. The focus was put on nonroad applications, construction and agriculture vehicles.
In his opening speech, Ander Hellman of Volvo Powertrain AB underlined the importance of integrated efforts to reach success in controlling future emissions. "The manufacturers, fuel suppliers, the users of the vehicles and the regulatory bodies need to work together to reach the goal," he said."New technologies have to be delivered at a pace never seen before,"Hellman added that he believed that the drive for ever-increasing engine power would come to an end, and expected that the engine produced in 2010 to 2015 will be down at very low emissions levels.
Independent consultant Michael P.Walsh's message concerned the importance of harmonizing emissions legislation in Europe, the U.S.A. and other regions, along with the importance of stringent CO2 and particulate emissions standards. His conclusion was that decisions made for Euro 6 would have broad global implications, as many high growth developing countries,including China and India, are following the European road map for heavy duty vehicles and engines.
"Technologies to achieve low PM (particulates), NO, and CO2 are available to make 'civilized' diesel engines,"said Walsh,Jose Pablo Laguna Gomez, directorate general for Enterprise and Industry, European Commission, pointed to the importance of introducing means to control the proper functions of systems like SCR.
Dr. Stephen J. Charlton, Cummins executive director of Heavy-Duty Engineering, listed the key technologies that have made the great progress in emission control possible "a near zero emission." He cited combustion technology, cooled EGR, high fuel pressure and flexible fuel injection.Another important feature is the single stage, variable geometry turbocharger, and eventually the aftertreatment of NOX and PM.
"However, the OBD,(on-board diagnostics), is a necessary and huge task, maybe as big as the emission issue itself," Charlton noted.
Hasse Johansson, group vice president, R&D, Scania, said its main path for Euro 5 is to develop EGR technology to be able to offer customers a broad choice of engines, without any need for after treatment and with a fuel economy similar to Euro 3 engines. Scania's recipe for Euro 5 is EGR with two-stage cooling, extremely high fuel injection pressure injection (up to 2400 bar), turbochargers with variable geometry,and the Scania in-house engine management system. "Since 10 years back,we have shared experience in the area of fuel injection and common rail with Cummins," he noted.
"Hybrid engines have a strong potential," Johansson added. "It would also be preferable to use available renewable fuels, like ethanol, FAME (fatty acid methyl ester), bio-based synthetic diesel and biogas." According to Johansson, the FAME could be mixed with diesel fuel from 5 to 100% and used in its engines, following consultations with Scania.
Phil G. Blakeman of Johnson Matthey gave an interesting overview of future NOX requirements and the SCR system options for heavy-duty diesel engines.He also discussed the new NH3 slip catalyst's contribution to NOX conversion at high temperatures.
"It is important to reach system durability," said Blakeman, "and the latest catalysts/systems demonstrate high thermal durability." It is also important to consider real engine aging for reliable judgment of a system's function,he added.
Stefan Becher, head of commercial engine test group, diesel systems,Robert Bosch, presented the contribution of fuel injection and air systems to advanced combustion concepts for heavy-duty diesel engines and underlined the importance of combining the two systems' efforts to reach optimal results. "For the long-haul truck market a non-aftertreatment strategy is not valid," Becher said.
Achim Dittler, chemical engineer,Daimler Chrysler, discussed the aspects for the Mercedes-Benz medium-duty engines, as developed meeting EPA'07 emissions standards. The EPA '07 aftertreatment device consists of a diesel oxidation catalyst (DOC) system and a diesel particulate filter (DPF). "The regeneration capability of the DPF represents a key operational functionality to meet system performance over a lifetime," said Dittler. "For a given DPF, with given material, size and exhaust flow conditions, the main application levers are maximum soot load, regeneration temperature and duration."
Concerning the Tier 4 legislation requiring a 90% reduction of NO, and PM emissions, Rolf Deisbach, head of diesel and powertrain mechanics engineering, MAN Nutzfahrzeuge, drew the some conclusion as many other speakers - that the maximum cylinder pressure will increase and consequently so will the fuel injection pressure. Electronic fuel injection systems are required to satisfy the need for flexibility of the injection system, and eventually cooling of the EGR system is needed.
"I see a dramatic increase of systemintegration work and application efforts to adapt to the requirements for improved cooling and charging," said Deisbach, "And standardization of systems will also be required to reduce costs and improve durability."
Akihiro Nishimura of the Yanmar Research Institute went through the broad variety of construction applications that engines have to satisfy."Special challenges meet the engines of construction applications," said Nishimura. "Examples are a dusty and severe environment, a problem of maintaining fuel quality and an extremely transient operation profile."
Danon Dou of John Deere Power Systems presented a paper on how the Tier 4 and Stage 4 diesel emissions regulations and a number of market requirements, like a quest for fuel efficiency and the generally harsh environment of off-road equipment, challenge the designers of next-generation off-road powertrain systems. "We need to provide customer value while meeting emissions requirements," said Dou. "We take a building-block approach at John Deere through system integration. The off-road industry may need to innovate beyond on-highway heavy-duty counterparts."
"To achieve Tier 4/Stage 4 emission levels, nonroad engine technology will merge with that of on-road engines," said Florentin Harrer, Iveco Motoren forshung. "SCR-type aftertreatment and particulate filters will be required, but also fuel and lubricants must be adopted accordingly and efforts done to meet different duty cycles and space constraints."
Claus F. Gorsmann of Johnson Matthey pointed to the DPF's capability of reducing PM emissions up to 90% and the ability of SCR and NOX adsorber catalyst (NAC) to affect NOX reductions up to 90%. "With the combination of PM and NOX control systems,the strongest emission requirements can be met," said Gorsmann.
Jim Faleffi of Caterpillar described how his company continues to develop advanced simulation tools from detailed combustion models to complete machine system applications, using these tools in engine and machine development programs. "We see that optimization of system designs, to meet more stringent emission standards, requires the use of system simulation to reduce development cycles," said Faletti. "Controls need to be an integral part of the simulation model, so they can be evaluated in terms of strategy and implementations of hardware."
Toward the end of the symposium Edward Jobson of the Volvo Group presented Volvo's hybrid technology. "There is an international trend toward long-term, non-incentive based, sustainable transports," he said. "London, for an example, has taken the initiative
to 100% hybrids for new buses by 2012.They will buy 800 buses per year. For Volvo, the parallel hybrid solution has been selected instead of a series hybrid solution."
According to Volvo, operation in the city center provided a fuel savings in the range of 30%, while in commuter service the savings are around 20%.The high torque at low speed is a stringent advantage and so is the lower noise emissions. The uptime for a hybrid
system is at least as high as for a diesel engine, Jobson noted.
Diesel Progress Magazine 2007